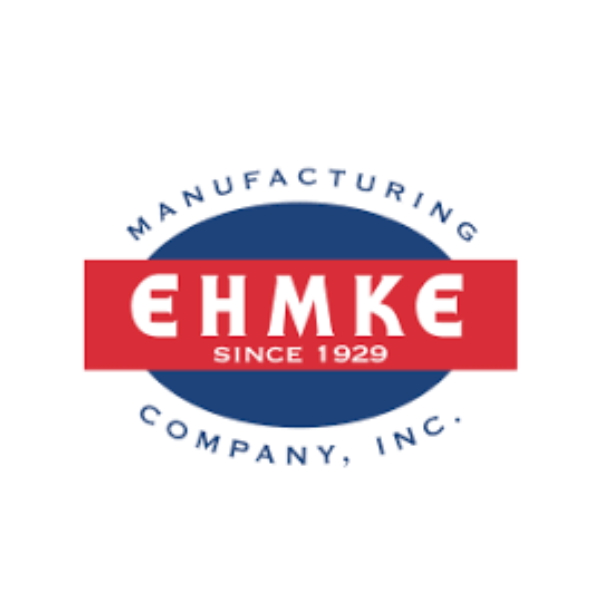
Background
Ehmke has been producing high quality industrial textiles products since 1929. Ehmke Manufacturing Company designs and fabricates a diverse range of technical fabric products for the US Armed Forces, its allies, the defense industry, and commercial OEMs for a host of industrial applications. The company is based out of Philadelphia, PA.
Situation
In early 2020, during the height of the COVID-19 pandemic, Boeing approached Ehmke Manufacturing Company with a large order, which necessitated a 10-25% increase in throughput. Ehmke’s traditional 3000 square-foot floor needed streamlining, and production capacity and throughput needed to increase.
Ehmke was no stranger to the value DVIRC provides, having worked with DVIRC several years prior. DVIRC worked closely with Ehmke’s team in the past to implement Cellular Just-In-Time (JIT) processes, incentives within the cells, and ERP software to help digitize data reporting. Now, tasked with such a large order, Ehmke knew who to turn to.
Solution
When DVIRC’s experts first engaged with Ehmke, they decided that the first step in shaping Ehmke’s culture was by training and educating the team about Lean processes. DVIRC provided every Ehmke employee with Lean 101 training, and five supervisor-level individuals completed DVIRC’s Level One Lean Certification course.
When Ehmke sought additional help from DVIRC to increase productivity to support Boeing, DVIRC’s Continuous Improvement expert Alan Shell took numerous employees through DVIRC’s Lean Tools and Essentials Course, which provides the essential tools needed to enable practitioners to implement continuous improvement processes at their companies. Further, he led Kaizen events, which are Continuous Improvement activities, focusing on incremental changes made by everyone in the organization by improving standardized activities and processes and eliminating non-value generating processes.
Shell helped draft Standard Operating Procedures (SOPs), which were created to help Ehmke’s team increase productivity and maximize efficiency by having standardized processes. Ehmke’s workspace was streamlined, quality inspection benches were shifted to optimized locations, and materials were repositioned as part of a key Lean tool – 5S – a series of activities designed to improve workplace organization and standardization, which involves going through all items and materials and then systematically sorting, cleaning and organizing them.
The training and stewardship provided by DVIRC over the years is nothing short of transformational for our company. The type of service delivered has helped prepare our company for sustainable growth. Thank you, Team DVIRC.
Bob Rosania, Owner/CEO, Ehmke
Results
Ehmke was able to realize the following results through its work with DVIRC, including:
- 5S processes led to a 900 square-foot increase in workable space to make room for new web cutting machinery
- 5S helped Ehmke avoid $50,000-$60,000 in costs
- 30% increase in cash flow
- 42% sales growth, and employee headcount did not need to increase to allow for this growth
- Boeing’s rigorous quality assessment standards were exceeded
- Year over year, Ehmke has increased revenue by $3 million
- The percent cost of labor was dramatically improved