We are excited to present Ken Baker, the latest addition to DVIRC’s board of directors. Ken is the CEO of NewAge Industries, a 100% employee-owned and B Corp Certified fluid transfer company. He brings nearly 40 years of experience to the board, including the manufacturing of tubing/hose and fitting, high purity fluid flow solutions, and RFID technology, both domestically and globally. In our conversation with Ken, we discuss his commitment to employee ownership, the remarkable 70-year evolution of NewAge, and his insights into the significance of the manufacturing sector.
Congratulations on recently joining DVIRC’s Board of Directors. What prompted you to devote your time and talent to this organization?
My advocacy for employee ownership led me to contact DVIRC’s president, Chris Scafario. Our discussions revealed a shared enthusiasm for employee ownership. Chris appreciated my perspective and was excited by the initiatives we have going on at NewAge as we seem to share a lot of the same visions for the future of manufacturing. Chris asked me to join and I accepted—that’s how my journey on the board began.
Speaking of employee ownership, can you expand on why you believe it makes a successful business model?
I think employee ownership is the right thing and the right capitalist way of doing business. My introduction to the model dates back to the mid-’90s when a seminar highlighted its potential. The appeal was in aligning everyone in a company toward a common goal. This unity, where success meant shared benefits, struck me as profoundly logical.
In 2006, I put my big toe in the water by allocating 30% of company shares to employees, or what’s known as an Employee Stock Ownership Plan (ESOP). The positive changes at NewAge were evident, and over time, as we became known as an employee-owned company. The move to ESOP significantly helped hiring efforts, employee retention, and overall process improvement, especially in contrast to private equity models in our space. Genuine care for employees is how you achieve a high-performance team.
NewAge is impressively nearly 70 years old. How has the company evolved over the years?
Oh, my gosh. Tremendously. NewAge’s first product line was metal hardness testing equipment imported from Italy. In the early ’60s, a fortuitous meeting led us into PVC tubing and hose, although we still weren’t making anything at that time. Over the years, we diversified, adding tubing lines and expanding into manufacturing in 1990. We ventured into high-purity silicone tubing for the pharma and biotech industries in 2000, marked by the sale of our hardness testing group. This allowed me to spend more time and concentration on the tubing product line. The subsequent decades saw further expansion into molding and assembly, and the introduction of ESOP in 2006. The strategic decision for a second site in 2000 and global expansion reinforced our commitment, notably during the pandemic as we heavily utilized the new facility to service the companies that were making the vaccine.
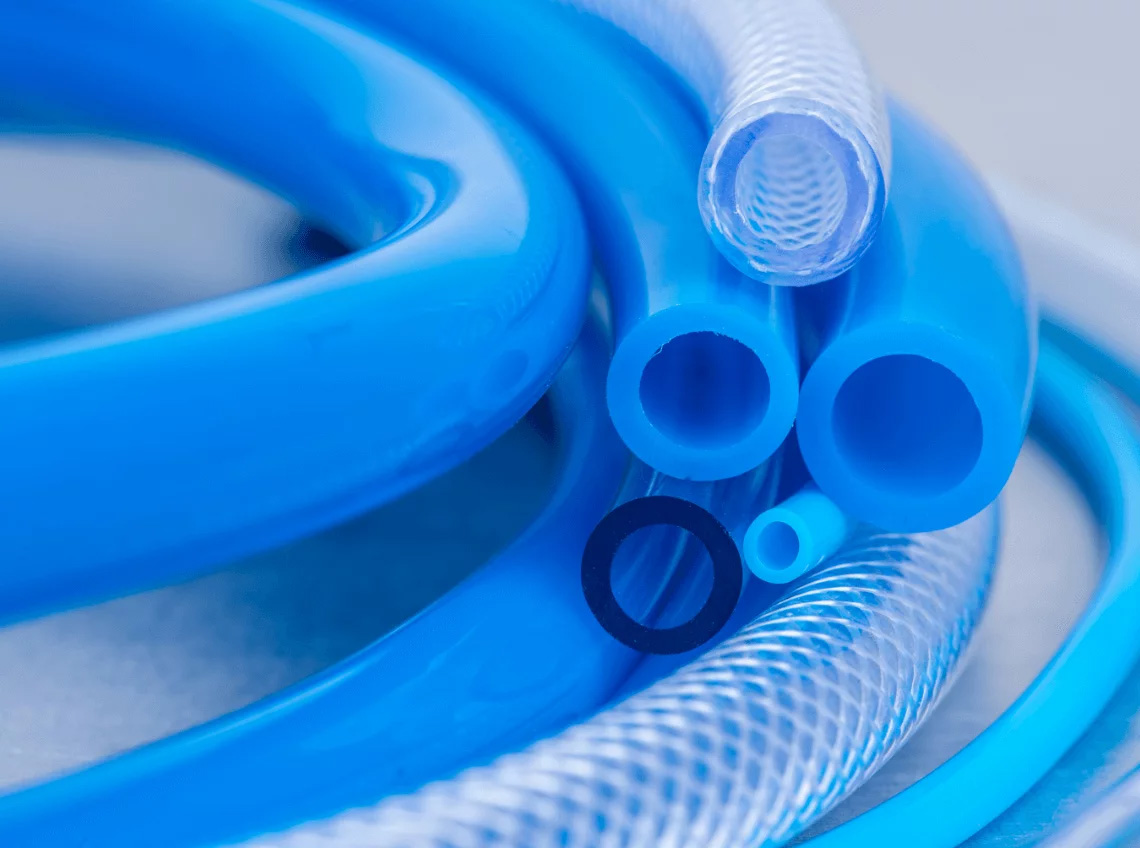
What do you envision for the next 100 years?
NewAge will not be sold. We will remain a 100% employee-owned, privately held company, leading in fluid transfer for pharmaceutical, biotech, and industrial applications 100 years from now. Our global footprint will expand, centered around the Netherlands, addressing the needs of the European and Asian markets.
What is it about your company and value proposition that makes NewAge unique to your employees, customers, and the markets you serve?
Quality is non-negotiable—you won’t compete without it but you won’t be distinct with it. NewAge’s differentiator lies in how we handle challenges. We set ourselves apart by being customer-centric: we are flexible, attentive to detail, and responsive to customer needs, not cookie cutter solutions. During the pandemic, our approach to cancellations—allowing for flexibility when other companies didn’t—is a testament to our customer-centric ethos. Other elements like our commitment to employee ownership, a no-layoff policy, and patented products contribute to our overall distinctiveness.
You’ve taken a step further by pursuing Certified B Corporation status. How does this align with your company’s values? And what motivated you to become a Certified B Corporation?
The pursuit of B Corp certification aligns seamlessly with our commitment to employee ownership and sustainability. NewAge has been green before it became a trend, and the certification validates our policies. It communicates to customers, vendors, and employees that we aren’t just claiming to be a responsible organization, we’re audited for it. The rigorous B Corp audit, with only around 3,500 organizations worldwide, reinforces our dedication.
Why should people consider a career in manufacturing?
Manufacturing is inherently creative and diversified. It’s about making things that impact our daily lives. From metals to plastics, ceramics to rubber, manufacturing spans a broad spectrum. Without it, we’d regress. Manufacturing is at the forefront of emerging technology, from 3D printing to automation. It doesn’t get any cooler than 3D printing—seeing a metal part made out of dust. But it’s not just cool; it’s essential for progress.
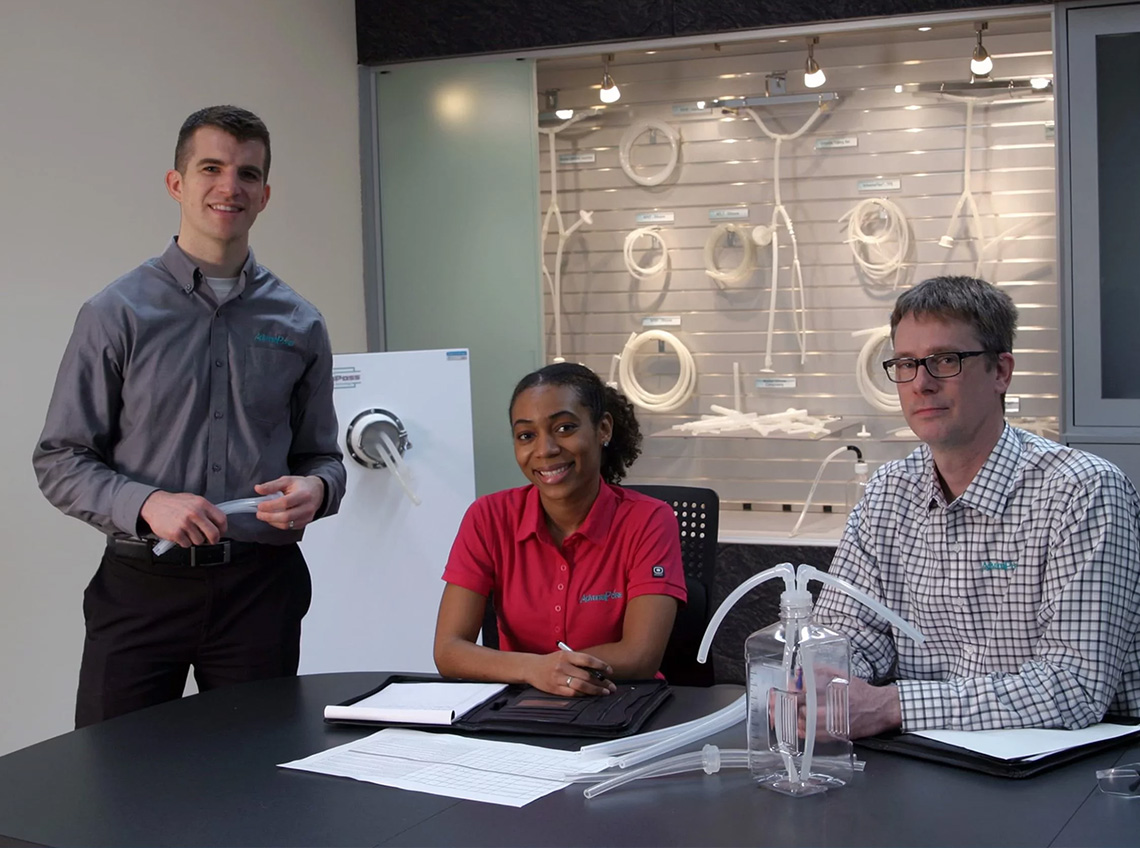
Any final words of wisdom for fellow manufacturing leaders?
Yes. Treat your employees with dignity and respect—it pays dividends in the short and long term. We otherwise diminish our capability as leaders.
Ken’s vision for NewAge reflects not only a commitment to excellence in the fluid transfer industry but also a dedication to employee ownership, sustainability, and quality-centric manufacturing. We are energized by our shared vision for manufacturing success and look forward to his strategic insights as a DVIRC board member. Ken’s knowledge and experience serve as a valuable guide for the future of manufacturing, starting here in Philadelphia.